36m TUBE
piles
29
marine &
land based
Construction
rediercted
Complex
Buried services
working
in an
Operational port
solutions
to
Licenced time limits
collaboration &
Value Engineering
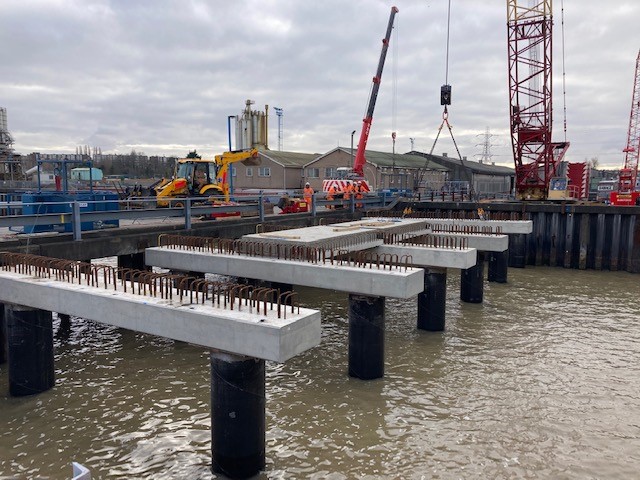
The Seacon jetty at Tower Wharf on the outer Thames close to Thamesmead was originally constructed in the 1950s.
It had come to the end of its design life and needed replacing. However, this is a multi-purpose facility for shippers of neo-bulk cargoes such as steel, metals and forest products, so was essential that operations continued undisrupted throughout our work.
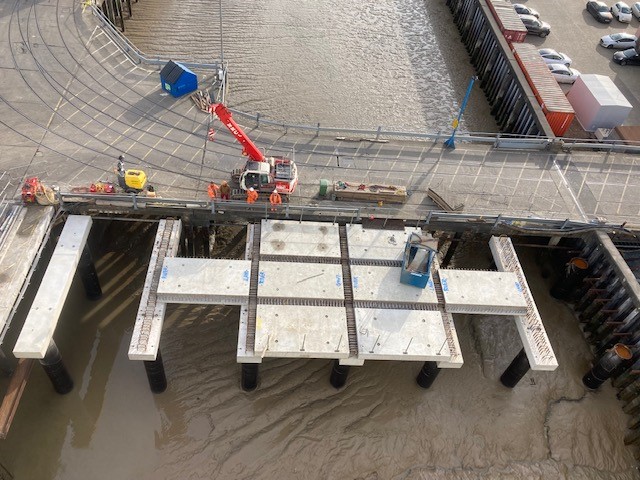
Our works involved:
- Diverting buried services and a power kiosk from beneath the new ramp footprint
- Installing 36m tube piles to support the new jetty and its ramp – 14 riverside, 10 landside and 5 king piles supporting the existing river wall.
- Building a bulk fill access ramp connecting the piled jetty structure and wharf access roads.
- Fitting pre-cast deck units to form the jetty substructure, then finishing with tarmac surfacing.
- Complex excavation behind the existing river wall.
We delivered these works while dealing with two major constraints: the MMO licence restricted piling to avoid harm to migratory fish and we had to keep Seacon’s adjacent jetty operating throughout.
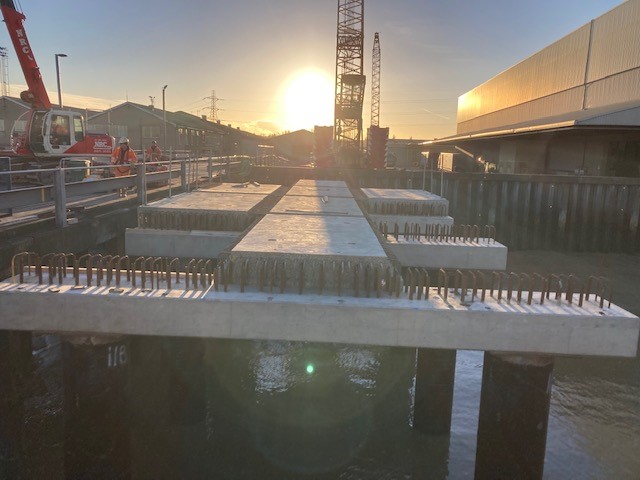
Early in the programme, the team found a large number of uncharted services underneath the main footprint of the jetty. Tracing and diverting these services would have resulted in a long delay, however our team came up with an entirely new access proposal that could be achieved in a shorter duration, still meeting the MMO restrictions.
Our engineers also worked with the designer and client to re-design the ramp, making it more stable on the very soft underlying ground conditions. Both solutions demonstrate our ingenuity and our approach of working with the designer and client to resolve project challenges.

Strengthening the wall required adding five 36m long 1016mm diameter anchor piles to the existing sheet piled wall, a separate wailing and new tie rods.
We constructed a bespoke piling gate to drive these piles accurately to avoid the existing tie rods.
They were installed in 2 phases to accommodate delivery by road (delivery by barge was not viable as this would severely disrupt the daily operations at the Main Terminal).
We drove the first 18m using an ABI piling rig; then the second 18m length was pitched and welded insitu. On completion of rigorous weld testing the full pile was then driven to depth by use of the more conventional crane and impact hammer. 14 of the seaward piles (7 rows of pairs) that support the new approach were driven as full 36m lengths. These were welded together and tested in advance on land within the site.
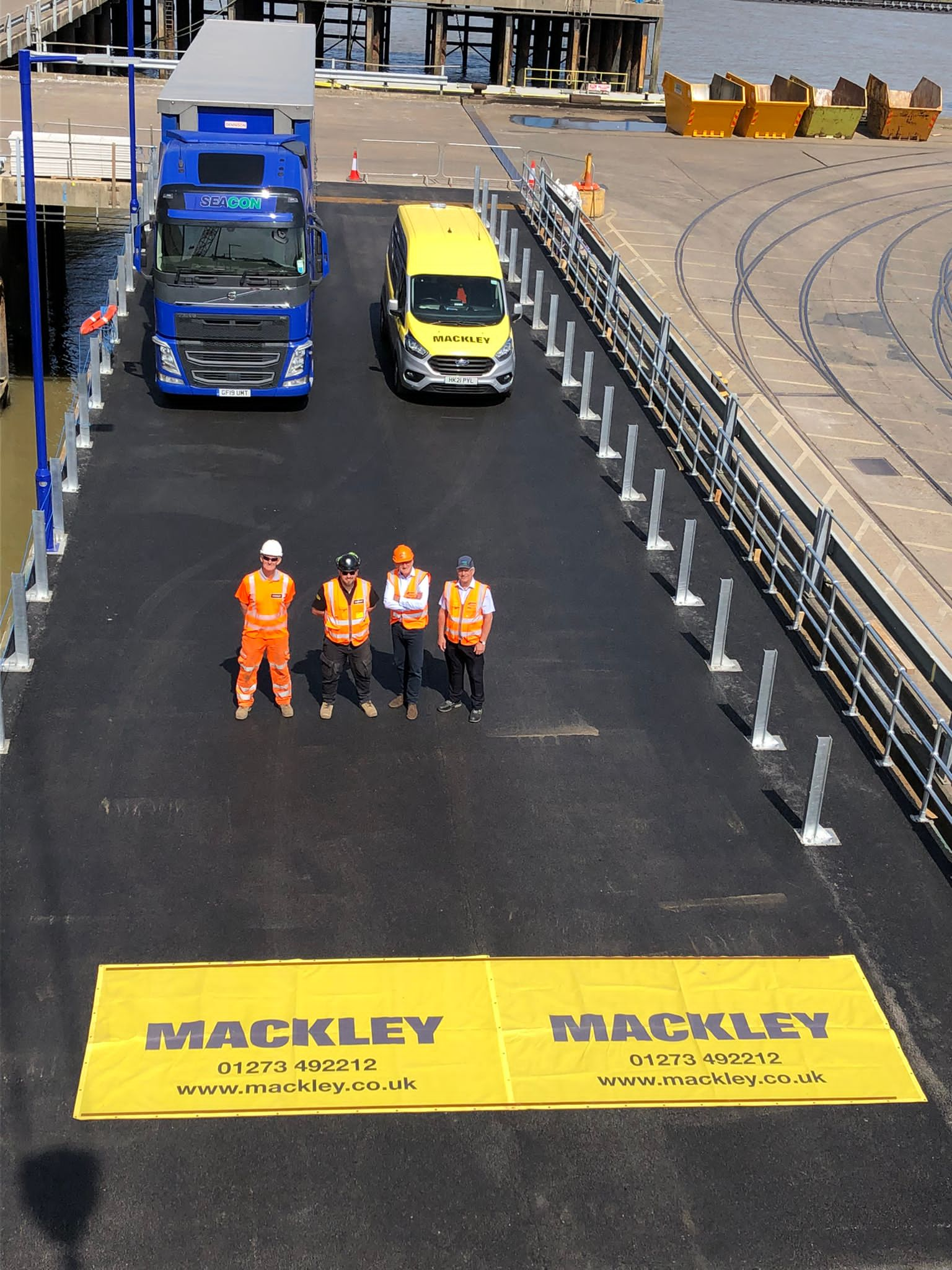
While the onsite welding was being carried out, we installed significant temporary works to construct a piling platform to enable a 400t Crawler Crane to carry out the seaward piling. Then to provide an additional safe access to work from, we brought in a modular Jack Up Barge, which was also used to lift in/out and support the piling gates.
With the piles driven to depth, work could begin to lift in the precast reinforced concrete cross beams, which were welded to the new tube piles. On completion of the welding the pile heads were grouted insitu.
New precast reinforced concrete slabs needed to be individually fabricated to ensure that the reinforcement interlocked. These were lifted on to the beams by use of the 400t crane on the landward side; after which further reinforcement stitch bars were installed and insitu concrete poured to form a monolithic jetty.
This was a challenging project that demonstrated some excellent engineering skills and big pieces of kit and materials